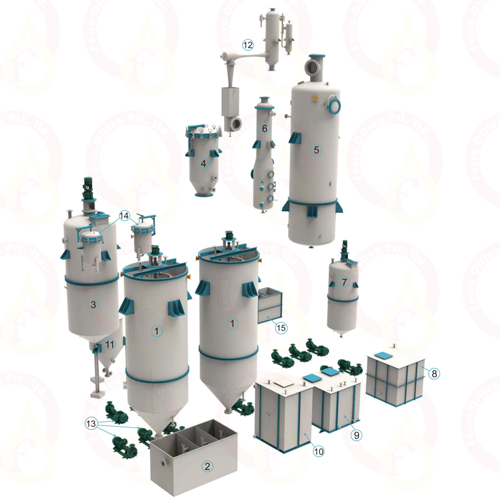
Batch Refining
Batch Refining, as the term suggests, is the process of batch refining capacities below 30 TPD.
Read More
Refinery
This is the second stage in Refinery plant. In this step, the oil is treated with caustic soda (sodium hydroxide) and free fatty acids are converted into insoluble soaps, which can be easily separated by centrifugation.
Thus, the main objective of this step is the removal of free fatty acids, although, as commented above, residual phospholipids in degummed oils or all the phospholipids in the crude oils are also removed as insoluble hydrates. Also, caustic neutralization improves significantly the oil colour partly by reacting with polar compounds and partly by solubilization. Alkali refining of oil is compulsory in crude oils of high acidity and pigment contents.
This separation of gums and soap from the oil is done by highly trusted MACFUGE equipment which are designed for centrifugal separation of solid-liquid, liquid-liquid-solid, liquid-liquid, in all its versions, types and materials. MACFUGE separator is a product of Servizi Industriali SRL located in Italy, is a partner with Ferro Oiltek for the supply of macfuge separator in India.
The free fatty acid content of the oil is the main factor that determines the amount and concentration of the caustic soda and also it excess for a minimum oil loss. After a reaction time of around 30 minutes at slow stirring and temperature around 75ºC, the water phase is eliminated by centrifugation and the oil washed with water to remove the remaining soap.
In Ferro’s Neutralization section, the main equipments are Reactor vessels, Caustic dosing tank, Phosphoric dosing tank, Knife-mixtures, Centrifuge separators, Plate type heat exchangers, etc along with various sub-parts like flowmeters, pumps, control valves, hot- and cold-water tank, strainers, etc.