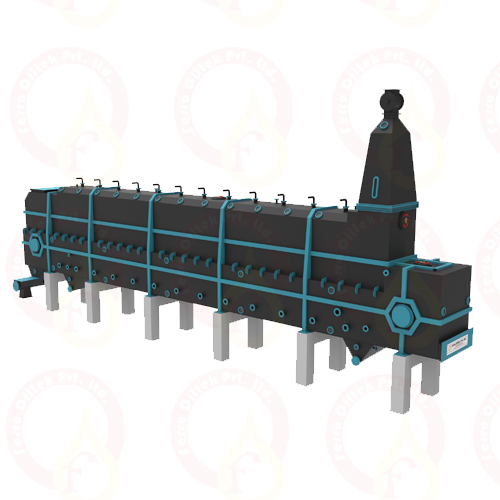
LM Extractor
In an LM Extractor, the material enters through an inlet hopper and is swiftly saturated with miscella.
Read More
Solvent Extraction
"Miscella" is the industrial term used for the oil/solvent mixture that leaves the solvent extractor. The miscella leaving the solvent extractor contains 70-80% solvent by weight. The purpose of distillation is to thermally separate the miscella into two things - a liquid oil fraction and a solvent vapour fraction. Optimum use of available heat in the discharge vapour stream from the de-solventiser toaster, the available heat from the condensate flash tank, and the heat recovery within distillation itself helps maximize the energy efficiency of the distillation process. The cooling tower & condenser are very important parts of distillation process.
Ferro provides a series of equipments that connected in sequence to provide heating of miscella at a certain temperature, to make sure the hexane from the oil is vaporized and also the oil should not over heated affecting it’s properties Ferro distillation unit collects these hexane vapours with the help of steam powered vaccum system which is highly efficient in working and it’s risk free. With Ferro Oiltek, optimum efficiency is achieved through perfection in size and design of the distillation equipment. The miscella tank is amply sized so that it acts as a perfect buffer after extraction to ensure the smooth flow through distillation. In our distillation system, we recover as much energy as possible by using various heat exchangers, economizers and so on.
The whole control of heating in distillation is done by providing severe control valves at the steam line of these heaters. These enable the automatic achievement of required temperature within the equipment. Depending on the client demand the Ferro can provide semi automatic as well as fully automatic extraction unit.
This design ensures a whopping 75% lower residual solvent in oil due to maximized steam/oil contact. This is due to its improved sieve-tray type oil stripper as opposed to the conventional disc/donut designs. In this design, there is a requirement for 15°C lower miscella temperature. This helps save second stage evaporator steam and reduces degradation of the crude oil prior to oil refining process. The 2-pass second stage evaporator design also enables fast miscella tube velocity and minimizes tube fouling and frequency of cleaning.