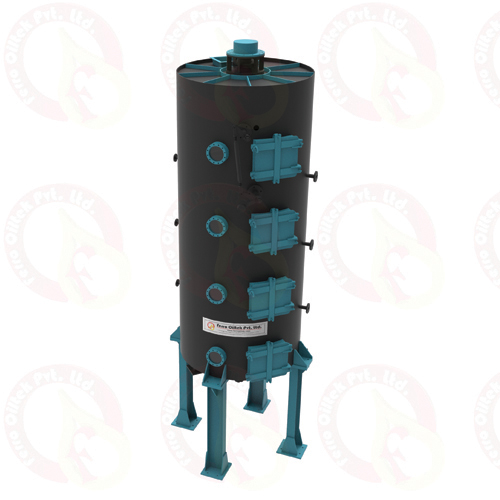
Cooker
The objective of cooker conditioning is to obtain the best conditions prior to flaking.
Read More
Seed preparation process is done for the preparation of oilseeds prior to Expelling or solvent extraction. This process basically includes: -
Cooking-conditioningThe important reason for conditioning is that the obtained flakes will contain fewer fines and will be more stable during the extraction process. By the injection of live steam into a vertical stack cooker, it is possible to adjust the moisture content of the conditioned seed. At this point the kernel should be at a temperature of about 50-75°C and a moisture content of 10.5-12%. It aims at obtaining, by means of cookers-conditioners, the best conditions prior to flaking by heating and adjusting the moisture content of the various oil-bearing materials to be subjected to prepressing or extraction processes for the removal of the fat contained therein.
Flaking
The conditioned seed is then flaked. By deforming seed particles into flakes, press and shear forces are created, which will rupture the seed’s oil cells, making them more available to the extraction process.
Expanding
Expander is designed to break the raw material into smaller pieces. In order to remove the oil, the solvent must permeate through the solid material and dissolve the oil out. Oil is trapped within oil bodies inside cellular membranes with added protection. So, the Expander machine not only break the oilseed into smaller particles, they also attempt to shear open the oil containing bodies within the cellular structure through mechanical shearing. The more shearing the material is subjected to and the smaller the particle size, the easier it is for the solvent to recover the oil. Expander flatten the material into a thin, round pellets to maximize exposed surface area. These pellets are then passed on to the Solvent extraction after maintaining its temperature & moisture content in Dryer-cooler.
Expelling
Expelling of oilseeds means a mechanical method for extracting oil from oil bearing seeds by physical pressure. It is cost efficient, versatile and chemical-free. Usually, we press the material firstly by Expeller machine and then get the rest of oil in the meal by using chemical solvent.
Drying & Cooling
As the name indicates, it provides drying and cooling of the meal before forwarding it to the Solvent Extraction. The cake/pellets came out of Expeller/Expander is fed to Dryer-cooler equipment. In drying section, hot air is blown through the conveying meal helping in reduction of moisture content within meal. Whereas in cooling section, cold air is blown through the conveying meal helping to reduce the temperature of meal, because the temperature of incoming meal plays a vital role in solvent extraction. The outlet temperature of Dryer-cooler is having to be below 50°C, hence dryer-cooler helps in maintaining the temperature as per need.
Note: We are not responsible for variation in production, because of irregular rainfall, due to which the seed gets damage and results in loss of production.
Preparatory Products Range
The objective of cooker conditioning is to obtain the best conditions prior to flaking.
Read More
Flakers function by means of flaking mills, which are equipped with smooth rolls.
Read More
When preparing oil seed meat (kernel) for further oil extraction, the kernel needs to be heated. Read More
Ferro Expanders are interrupted flight screw machines that generate a high pressure.
Read More
The Ferro Expeller is a self-contained unit which has its own heating kettle or conditioner.
Read More
The vibro separator is suitable for all types of screen operations with below stated four broad categories. Read More
The Pressure Leaf Filter is a MS Vertical Vessel with Filter Leaves inside.
Read More
Ferro Filter Press offers excellent filtration parameters at low running cost and purchase price
Read More
The machine comes with one feed module and an unload one with additional intermediate modules for drying and cooling.
Read More
The machine comes with one feed module and an unload one with additional intermediate modules for drying and cooling.
Read More