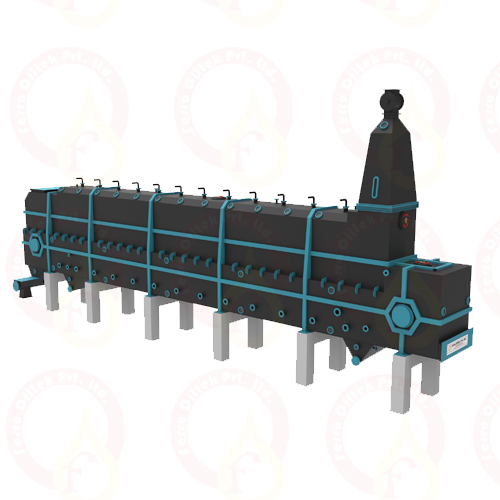
LM Extractor
In an LM Extractor, the material enters through an inlet hopper and is swiftly saturated with miscella.
Read More
Solvent Extraction
Our DT has six stages (can vary according to plant capacity or requirement) with top two stages for de-solventizing and subsequent stages for toasting without over heating to give light colored meal free of solvent and high in protein content. The meal exiting the extractor contains 30-35% solvents by weight. The meal is thus heavily solvent-laden and the purpose of the de-solventizing process is to remove the solvent. The goal is also to toast the meal so that antinutritional factors are controlled, and the moisture and temperature of the meal is reduced to levels appropriate for storage and transport. Live steam is condensed and latent heat is used to supply most of the heat supplied for evaporating the solvent from the meal. This simultaneously increases the moisture in the meal to facilitate toasting. Air is passed through a fluidized bed of meal and this way, drying and cooling of the meal is accomplished. Before passing on to distillation for heat recovery, the solvent and water vapours exiting the de-solventizing process, pass through a scrubber to remove meal particles.
In our DT, the steam provided within DT chambers are controlled by automatic controlled valve. Hence chances of over heating and incomplete heating is reduced to meal. At each stage, the bed heights are controlled by vapor tight, carbon steel construction with numerous stages; and a bottom driven drive-mechanism with mechanical float and door system. The shaft is centrally driven with specially designed scrapper with a hardened face. There is also a provision for specially designed sparge trays to add steam open steam so that hexane losses are minimised. It also includes a precisely designed duct of vapor. The entire de-solventization process takes place with the help of direct and indirect steam.
From the DT, the cake is either conveyed to a dry cooler or in case of ferro the passed directly into drying section of the DC (Dryer Cooler). The Drying & Cooling are accomplished by blowing heated air in the drying section or using ambient air to cool the meal in the cooling section.